ลวดเชื่อม MIG รุ่น ER70S-6 1.2mm (15kg) SUMO
ลวดเชื่อม Mig ER70S-6 เป็นลวดเชื่อมมีคุณสมบัติที่ดีทางกล ให้ชิ้นงานรูปทรงดี สะเก็ดติดโลหะน้อย เชื่อมนิ่ม ทนต่อแรงดึงได้ถึง 540 Mpa
- สำหรับการเชื่อมแบบมิกแมก (MIG/MAG) ได้ดีในทุกท่าเชื่อม
- ลดการสึกหรอและยืดอายุการใช้งานของหัวทิปลวดเชื่อมมิกมีปริมาณซิลิกอนสูง
- มีส่วนผสมของ ฟอสฟอรัสและกำมะถัน ทำให้ลวดเชื่อมมีความแข็งแรงทนทาน ทนต่อการกัดกร่อน
- ช่วยให้แนวเชื่อมสวยงาม และมีปริมาณสะเก็ดโลหะต่ำในขณะเชื่อมเหมาะเป็นอย่างยิ่ง
- สำหรับการเชื่อมโลหะที่มีความหนาน้อยถึงปานกลางรวมถึงงานท่อทั่วไป
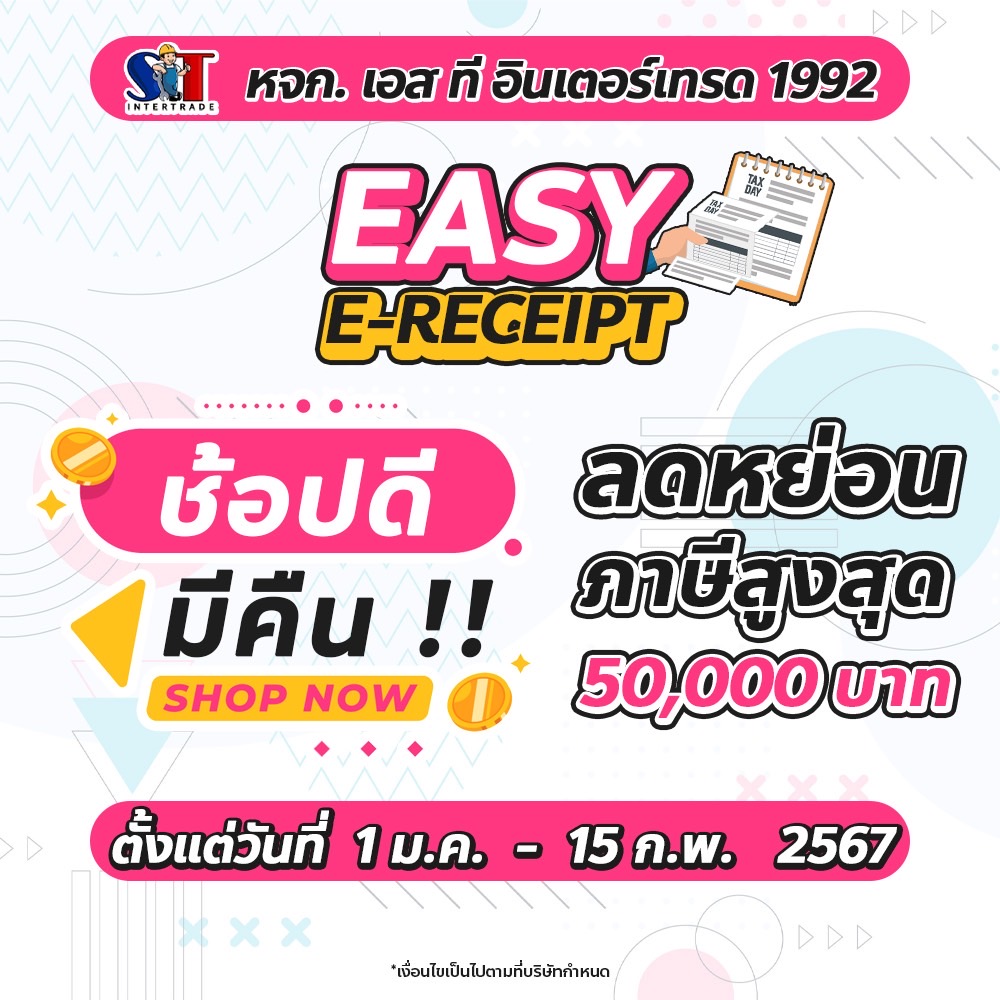
สนใจสอบถามเพิ่มเติม
รายละเอียดเพิ่มเติม
ลวดเชื่อม MIG รุ่น ER70S-6E 1.2mm (15kg) SUMO
ER70S-6E Welding wire 1.2mm (15kg) SUMO
A general purpose of welding wire with copper coated for long contact tip life is provides superior feeding and arc stavility design for fabrication of mild steel. Contains higher level of manganese and silicon than the other standard grades of MIG wire, provides superior feeding and arc stability design for fabrication of mild steel. Contains higher levels of manganese and silicon than the other standard grades of MIG wite, provide high deoxidizers to heavy mill scale surfaces that provide better wetting, yielding a flatter bead shape and the capability of faster travel speeds. Usually used with 75/25 (Argon/Co₂) shielding gas or higher contents of Argon, such as 90/10. Can also be used with 100% Co₂. Conforms to AWS A5.18 ER70S-6E.
Feature
- Consistent welding performance
- Stable arc with low feeding force
- Excellent arc ignition
- High current applicability
- Extremely low overall spatter
- Low fume emission
- Trouble-free feed ability, even at high wire feed speeds and lengthy feed distances
Applications
- SUMO ER70S-9E It is a great choice for welding light to moderately scaled, oily or rusty plates. It can also be recommended for spray transfer arc welding applications. Used for butt and fillet welding of sheet and plate of a variety of thickness. Applications included general carbon steel fabrication.
Shielding gas
- 100% CO₂
- 75-95% Argon / Balance CO₂
- 95-98% Argon / Balabce O₂
- Flow Rate : 35-50 CFH
Guideline for use
- Oil stanins and rust must be removed from surface of weldment prior to welding in accordance with appropriate welding standards.
Storage
- Product should be stored in a dry, enclosed environment, and in its original intact packaging.
Electric shook can kill
- Insulate welder from workpiece and ground using dry insulation. Rubber mat or dry wood.
- Wear dry, hole-free gloves. (Change as necessary to keep dry.)
- Do not touch electrically “hot” parts or electrode with bare skin or wet clothing.
- If wet area and welder cannot be insulated from workpiece with dry insulation, use a semiautomatic, constant-voltage welder or stick welder with voltage reducing decice.
- keep electeode holder and cable insulation in good condition. Do not use if insulation damaged or missing.
Welding sparks can cause fire or explosion
- Do not weld on containers which have held combustible materials (unless strict AWS F4.1 procedures ard followed). Check before welding.
- Remove flammable materials from welding area or shield from sparks. heat.
- Keep a fire watch in area during and after welding.
- Keep a fire extinguisher in the welding area. Wear fire retardant clotging and hat. Use earplugs when welding overhead.
Arc rays can bur eyes and skin
- Select a filter lens which is comfortable for you wgile welding.
- Always use helmet when welding.
- Provid non-flammable shielding to protect others.
- Wear clothing which protects skin while welding.
Fumes and gases can be dangerous
- Use ventilation or exhaust to keep air breathing zone clear. comfortable.
- Use helmet and positioning of head to minimize fume in breathing zone.
- Read warnings on electrode container and material sadety data sheet (MSDS) for electrode.
- Provide additional ventilation requriements exist.
- Use special care when welding in a confined area
- Do not weld unless ventilation is adequate.
Confined space
- Carefully evaluate adequacy of ventilation especially where electrode requires special ventilation or where gas maydisplace breathing air.
- If basic electric shock precautions cannot be followed to insulate welder from work and electrode. use semiautomatic, constant-voltage equipment with cold electrode or stick welder with voltage reducing device.
- Provide welder helper and method of welder retrieval from outside enclosure.
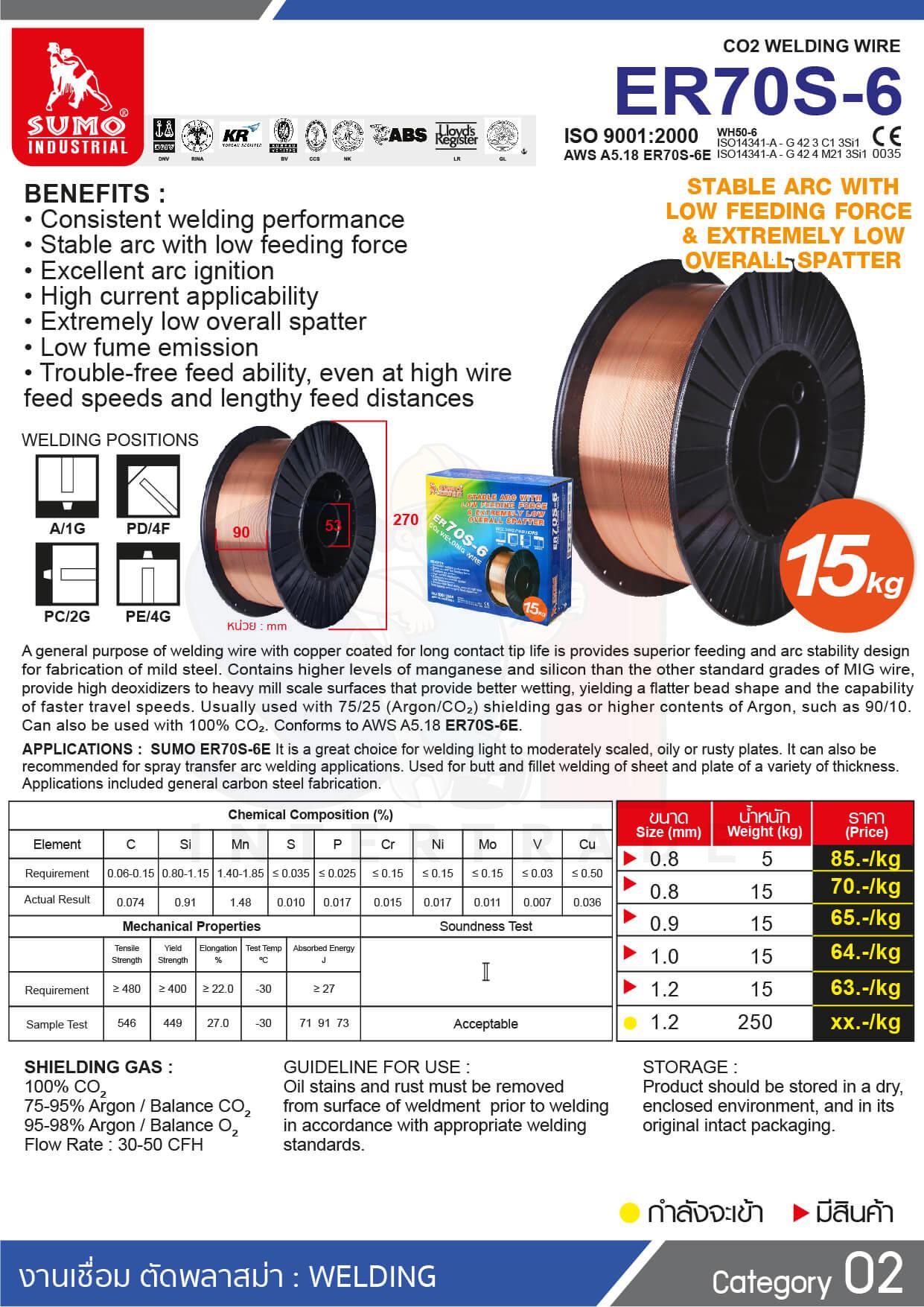